The seeds are sown for the electrification of farming vehicles, but as major manufacturers begin to develop electric prototypes, they face major logistical challenges to replacing diesel-burning machines in the field.
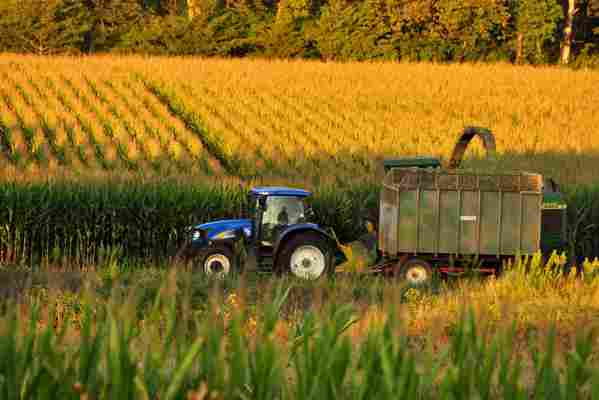
“The critical piece of the pie for greater adoption of electric vehicles in farm settings is charging infrastructure, followed closely by durability and reliability issues,” said Scott Miller, associate dean for industry partnerships at Ohio University’s Russ College of Engineering and Technology. “Farmers will not abide things that they cannot fix quickly, cheaply and easily.”
Modern agriculture depends on a fleet of heavy-duty vehicles and machinery, from pickup trucks and small utility vehicles to massive tractors and combines that can weigh from a few tons up to as much as 15 tons, plus attachments. All that weight, along with dawn-to-dusk workdays and multiple worksites, adds to the challenges of electrification.
“Today the reason why most agricultural machinery is [run by] diesel is because of the high power-to-weight ratios when we look at energy storage in the form of diesel fuel,” said Scott Shearer, chair of the Department of Food, Agricultural and Biological Engineering at Ohio State University. Large equipment “can work all day without having to refill.”
Although diesel power is dominant now, the market for electric vehicles in the construction, agriculture and mining industries could grow to $100 billion annually, according to analysts Peter Harrop and Michael Dent at IDTechEx, headquartered in England.
It’s still unclear precisely what mix of incentives, regulations and market forces might drive the transition to electric farm equipment, but countries will need to address the sector in order to achieve emissions reductions on a large enough scale to avert worst-case climate change scenarios this century.
The Intergovernmental Panel on Climate Change’s latest report, released on Aug. 9, underscores the need for immediate steps to cut greenhouse gas emissions. Agriculture accounted for about 5% of U.S. industrial energy consumption last year, according to the Energy Information Administration.
Technological innovation could also spur demand for electric vehicles on the farm. Small electric tractors could be particularly helpful for family farms in developing regions that still use non-mechanized methods for agriculture, according to an August 2021 report in the Journal of Energy Storage.
Larger companies that make farm vehicles generally sell to global markets. So developments in other regions will likely affect the range of product offerings worldwide.
Additionally, farmers in Ohio and elsewhere could be drawn to the idea of replacing diesel with on-site renewable power, particularly those who have already leased part of their land for solar or wind energy in order to boost income. As the costs of renewable energy and battery storage come down, electric vehicles could eventually lower energy costs for farms.
On the drawing board and in the field
Mindful of the clean energy transition, multiple companies already have been working on electric-powered prototypes.
John Deere’s concept model tractors would allow autonomous operation, which increases efficiency and precision. Cable power could even eliminate the need for onboard batteries, so that an electric version need not weigh more than its fossil-fueled counterpart. A John Deere spokesperson declined to be interviewed for this article.
Japan-based Kubota also introduced concept models in January 2020. Like the Deere models, they would allow autonomous operation. And triangular track arrangements could minimize weight and adjust for height in the field. The company’s concept tractor also featured an onboard solar battery.
California-based Solectrac already has been offering small 30- and 40-horsepower-equivalent tractors and farm utility vehicles. Other options for relatively small tractors come from Fendt, Rigitrac, Escorts and others. Meanwhile, almost all airborne drones are electric.
Solar power could benefit a range of agricultural machinery beyond charging tractors, according to an April 2021 report in the Journal of Cleaner Production.
“We’re beginning to see some agricultural sprayers that are actually operated with photovoltaics,” Shearer said. An autonomous weed-control robot from Swiss-based ecoRobotix aims to use 95% less herbicides, for example.
Research also is focusing on small electric ground-based autonomous vehicles for sensing the plant environment. But field navigation could still be tricky, Shearer said. Challenges include working through plant rows, such as picket-fence formations used in cornfields, and dealing with plant canopies.
Challenges ahead
But it’s a big step to go from prototypes and limited applications to widespread adoption.
“Farm equipment may only get used a few weeks a year,” and those periods of use often run “up to 15 hours a day for many days on end,” Ohio University’s Miller said. “It does a farm producer no good if the battery runs out in the middle of a 1,000-acre field.”
If batteries provide only about 15% of the energy that a full tank of diesel does, “you’re still going to have to stop six or seven times a day,” to swap out batteries, Ohio State’s Shearer said. With spring planting time at a premium, the opportunity cost for those stops’ lost productive time could run into thousands of dollars.
Adding bigger batteries isn’t the answer, either. The additional weight can compact soil more than existing equipment does. The result could be less room for young plants’ roots to grow, said Dale Arnold, director of energy, utility and local government policy for the Ohio Farm Bureau Federation.
Compacted soil also can interfere with no-till methods that many farmers have been using, Arnold added. No-till farming leaves more organic material and nutrients in the soil. The practice also lets more water infiltrate the soil, resulting in less runoff and nutrient pollution.
The key is trying “to find that balance” that lets machinery do work efficiently, without adding more steps or hurting farm yields, Arnold said. Also, many farmers’ fields aren’t contiguous.
“There are times where a large piece of equipment — a large tractor or a combine or a large cultivator — might leave home base and might not return for several days or a couple of weeks, based on the complications and the activities there,” Arnold said.
Arnold’s own family still farms the Brown Township property in central Ohio that belonged to his grandfather. The family also acquired farms in Harrison Township and Union Township, he said. Typically, farm equipment would work on one farm property. Then it would travel to the next property and the next, before returning to home base days or weeks later. The cycle would repeat for the next necessary tasks.
“You’re always in that rotational schedule,” Arnold said. “Many farm families, that’s what they do.”
So, even if large electric farm equipment could run for a full day on a battery charge, it wouldn’t necessarily return to home base at night. That situation would add to the costs and challenges of charging infrastructure. And more stations would be needed in any case, Arnold said, because lighter-weight pickups or other off-road utility vehicles also would need charging.
“The one key issue is going to be breakthroughs in battery technology,” Shearer said. In his view, even an increase in battery power to half the energy delivered by the equivalent weight of diesel fuel could be “a game-changer.”
In the meantime, registrations for Ford’s first all-electric pickup truck opened in May with the introduction of the F-150 Lightning. Lordstown Motors’ planned electric pickup truck also could be a big winner, Arnold said, if the company manages to overcome financial problems. On Aug. 11, the company announced plans to begin limited production in September.
“We feel that’s going to be a very competitive market,” Arnold said, noting that almost every farmer has a pickup truck, as well as smaller utility vehicles.
Wi-Fi connectivity is an additional challenge. Autonomous navigation and controls, on-board diagnostics, and other equipment devices will “depend on good high-speed communications with base stations or the internet,” Miller at Ohio University said. Manufacturers also will likely move toward more cloud-managed solutions and software-as-a-service business models, he added.
“As we know, rural broadband is a huge limiting factor for rural communities,” Miller said, “so these sorts of models will take time to implement and may require creative partnerships with major tech companies to overcome these connectivity hurdles.”
The Reimagine Appalachia coalition also has been calling for major upgrades to rural areas’ broadband and electric infrastructure as part of a plan for transitioning away from dependence on coal and natural gas. The group is pushing for funds to come from federal infrastructure grants.
In the meantime, niche areas for smaller vehicles and equipment could expand more quickly. And manufacturers of larger equipment will refine and test prototypes to make sure they can perform as well in the field as they might on the drawing board.
A specific time frame for widespread adoption of electric vehicles on farms remains undefined. Climate advocates generally want emission cuts to come sooner, rather than later. And if the world indeed shifts to net-zero greenhouse gas emissions within the next few decades, equipment manufacturers will want to continue to meet farmers’ needs.
Ultimately, “farmers are interested in tools that will help them increase yields and productivity,” Miller said. “The upside, hopeful note is that these tools have the potential to transform the method and manner in which agricultural producers manage their lands and crops by increasing efficiency and using their limited resources as wisely as possible.”